Screw Press – Operation, Applications, and Their Contribution to Recycling
It's a common challenge in the metalworking industry: large quantities of grinding sludge and other types of sludges are generated during the processing, and disposing of them can be costly. The high liquid content, in particular, drives up disposal expenses due to the significant increase in volume. Additionally, there are expenses associated with replenishing the disposed liquid. One solution to reduce these costs is the use of screw presses. Integrating these multifunctional pressing systems enhances both the cost-effectiveness and sustainability of the production process. In this article, we explain the function and operation of screw presses and explore the areas in which they can optimize your production.
What is a Screw Press?
A screw press is a pressing machine used for both dewatering solid-liquid mixtures and compacting solid materials. In German it is also known as ‘Schneckenpresse’. They derive their name from a screw conveyor, which serves as the central component of these presses. In essence, the operation of a screw press involves rotating the screw to exert pressure against a resistance, compacting the material and potentially dewatering it. For this reason, they are also referred to as screw compactors. We will look at how exactly this press works in detail below.
The function of a
screw press
In this section, we will explain the construction and operation of screw presses using our FSP press type. This type of presses is primarily designed for dewatering solid mixtures such as industrial sludges. Although the specific construction may vary among manufacturers and application cases, the basic operation remains similar for all presses of this kind.
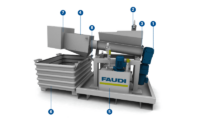
At the start of the process, the material to be dewatered is placed into the filling funnel (2). This is when the characteristic screw conveyor (3) comes into action, driven in rotation by a gear motor (1). It continuously conveys the material through the rotational motion to the so-called dehydration area (4).
In our FSP presses, this dehydration area consists of a slotted sieve cylinder, the outlet opening of which is closed by a spring-loaded pressure plate. The pressing process is achieved through the continuous material feed, which results in the compression of the material to be dewatered. Thus, this action effectively extracts the liquid.
After that the liquid flows out through the drain opening (8) and can be collected. So the dewatered material is discharged as follows: The increasing pressure in the dewatering section shifts the pressure plate above the slotted sieve cylinder, opening an outlet in the area of the sludge discharge (7) above a container (6). After that the dewatered material falls into the container. And subsequently, the pressure springs return the pressure plate to its original position, closing the outlet once again. Optionally, the dewatering screw can be equipped with a return pump station (5).
Where are these presses
used?
Undoubtedly, this type of industrial presses can be beneficially applied in various sectors. Especially, screw presses designed for dewatering or oil removal are used in the automotive industry, machine tool industry, aviation industry, and other metalworking sectors. They are utilized for dewatering or dehumidifying grinding sludges, sewage sludges, and any other sludges generated due to production processes.
Additionally, in the same industries, screw presses function as pre-dewatering equipment for (metal) chips and sludges to prepare them for further processing through a briquetting press. Consequently, this boosts throughput performance and briquette quality.
Other areas of application include the food and cosmetics industries, where screw pressing is used for obtaining cold-pressed oils or producing fruit juices. They are also used in agriculture, for instance, for sludges with plant residues. Moreover, they find application as compactors in the paper industry.
In general, highly concentrated solid mixtures, due to their high compressibility, are easier to process. Thin suspensions may need thickening using flocculants before pressing.
However, there are versions of the press that do not include the dewatering function. The primary function of these screw presses is compacting solid materials, such as dry waste like cardboard and foil in the waste industry. Due to that their volume for transportation can be reduced.
Enhancing Material
Recovery
Regardless of the sector where screw presses are used, they reduce the volume of residual materials. This results in making transportation easier and decreasing disposal costs.
Dewatering screw presses provide an additional essential benefit that is the recovery of valuable fluids such as emulsions and oils. Therefore, these fluids can be immediately returned into the production process at the end of the pressing process. Advantageous is that such solutions can achieve fresh oil savings of up to 95%. Thus, the presses not only reduce the costs associated with purchasing fresh fluids but also promote a more closed and environmentally friendly production cycle.

To better understand the scale of these savings, let’s consider two example calculations. In these calculations, our FSP press is used for dewatering grinding sludge. With a remaining material quantity of about 500 tons (250 tons of solids, 250 tons of oil/emulsion), an estimated savings of approximately 143 tons of oil or emulsion (about 57%) can be expected. For that reason, this represents a significant cost reduction achieved through savings on fresh oil and emulsion concentrate. Additionaly, it leads to further savings through reduced disposal costs. The actual cost savings will naturally vary based on the properties of the residual material and the press configuration. Nevertheless, using a screw press proves to be a sound investment in most industries where wet residuals are generated.
Interested in optimizing your material recovery?
Learn more about our screw presses here.
Additional Measures for
Material Recycling
Screw presses work well as an economical standalone solution. However, further opportunities for material recycling arise when combining them with briquetting presses.
This is because the pressing performance of briquetting machines greatly depends on the fluid or residual moisture content of the material being briquetted. As a result, sludges, particularly grinding sludges, still pose a significant challenge in the briquetting process. Screw compactors can provide optimal support here. Thanks to their pre-dewatering, sludges can be processed more efficiently.
It is clear that the combination of screw and briquetting presses enables the maximum dewatering and subsequent briquetting of grinding sludges, slags, and dust of all kinds. Metal chips like copper, steel, or magnesium chips are processed, as well. In addition, the highly compacted, manageable chip briquettes can be sold to waste disposal companies at higher returns. And this converts production residuals into usable secondary raw materials.
Combining with Filtration Solutions
Combining screw presses with filtration systems is also possible. In fact, this solution is especially suitable for coolant treatment. Together, filtration systems and presses ensure the best possible recovery and reuse of cooling lubricants and a more environmentally friendly handling of residuals.
All of our presses are compatible with our in-house filtration solutions, as well as those from popular manufacturers. This means that existing systems can also be retrofitted with screw compactors and briquetting machines.
Conclusion
In metalworking industries, the generation of chips, slag, and sludges is inevitable due to the nature of the processes. In summary, screw presses provide an economical and ecological solution that significantly reduces industrially generated production residuals and closes the material cycles. From dewatering and oil removal to compaction and material recovery, the functions and applications are diverse. For example, in combination with other presses and filtration systems, additional possibilities for use emerge. This allows the maximization of cost-effectiveness and environmental compatibility within the production process.
If you are seeking a solution for your material recycling, we are here to advise you.